Top Innovations in Radiator Plastic Tank Manufacturing
- linghangtech
- May 12
- 3 min read
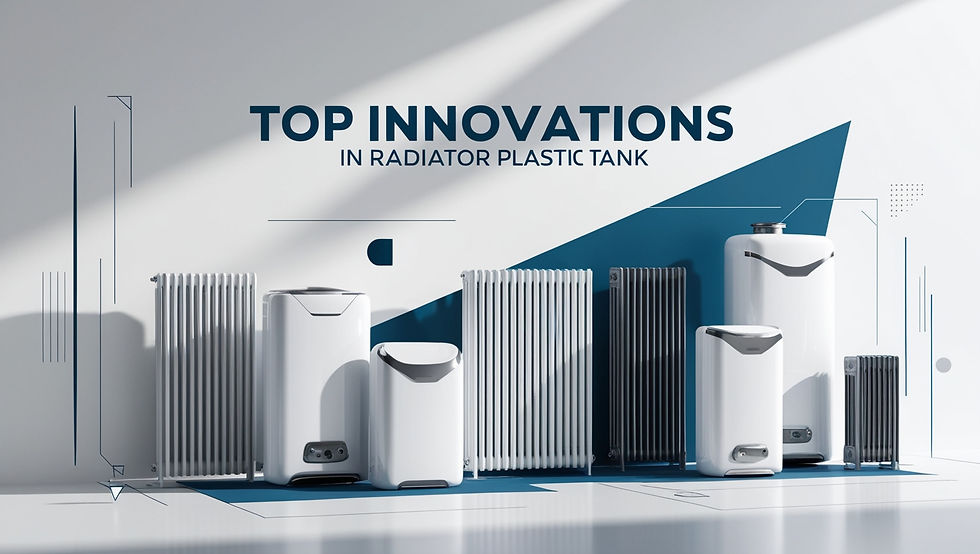
When you think of car cooling systems, your mind probably jumps straight to radiators. But did you know the radiator plastic tank plays a key role in keeping your engine cool and performing at its best? Over the past decade, the way these plastic tanks are manufactured has evolved in some seriously impressive ways.
Let’s take a deep dive into the top innovations in radiator plastic tank manufacturing that are making vehicles more efficient, durable, and cost-effective today.
1. High-Performance Polymer Materials
One of the biggest game-changers in plastic tank manufacturing has been the use of advanced polymers. Modern radiator tanks for cars are no longer made from basic plastics. Instead, manufacturers now use high-strength, heat-resistant materials like glass-reinforced nylon or polyamide composites.
These upgraded materials can withstand extreme engine temperatures and high-pressure conditions without cracking or degrading—something older plastics simply couldn't handle.
2. Integration of Blow Molding Technology
Traditional injection molding is slowly being replaced or complemented by blow molding techniques. Why? Because blow molding allows manufacturers to create hollow, seamless, and complex tank shapes with uniform wall thickness, which improves the tank’s durability and thermal efficiency.
This method also reduces production waste, making it an eco-friendly option in the long run.
3. Laser Welding for Leak-Proof Assembly
Remember when leaking radiator tanks were a common headache? Not anymore. Thanks to laser welding technology, plastic radiator tanks are now sealed with incredible precision, leaving no room for leaks.
Laser welding creates strong, clean joints between parts, ensuring the tank can withstand pressure changes and vibrations without splitting at the seams.
4. Smart Sensor Integration
The modern radiator plastic tank isn’t just a container anymore—it’s getting smarter. Some of the latest designs now include built-in sensors that monitor:
Coolant levels
Temperature
Pressure variations
This kind of real-time data helps car owners and mechanics spot issues before they turn into serious engine problems. Talk about taking preventive maintenance to the next level!
5. Lightweight Construction for Better Fuel Efficiency
One of the auto industry’s major goals is reducing vehicle weight to improve fuel economy. Radiator plastic tank manufacturers have stepped up by creating lighter yet stronger tanks using optimized material blends.
This not only boosts vehicle efficiency but also reduces emissions—something both manufacturers and consumers are now prioritizing.
6. Modular and Customizable Designs
Gone are the days of one-size-fits-all tanks. Today’s tanks are often modular and vehicle-specific, meaning they can be tailored to fit a particular model or even a custom engine configuration.
This flexibility helps OEMs (Original Equipment Manufacturers) streamline production while ensuring perfect compatibility and performance.
7. Enhanced UV and Chemical Resistance
Plastic radiator tanks are exposed to some pretty harsh conditions under the hood—UV rays, oil vapors, and aggressive coolants. New coatings and chemical-resistant polymers now offer superior protection against UV degradation and chemical corrosion.
That means longer-lasting tanks, fewer replacements, and happier vehicle owners.
8. Environmentally-Friendly Manufacturing Practices
Sustainability is no longer optional—it’s a necessity. Many top manufacturers now use recyclable materials and eco-conscious processes to produce radiator plastic tanks.
From reducing water usage during molding to incorporating post-consumer recycled plastics, the shift toward greener manufacturing is well underway.
9. 3D Printing and Rapid Prototyping
Yes, even in radiator tank manufacturing, 3D printing is making waves. Engineers now use 3D prototyping to test and fine-tune designs before committing to mass production. This helps:
Cut down on production time
Reduce design errors
Speed up innovation cycles
It’s a win-win for both manufacturers and consumers.
10. Improved Quality Control Through AI and Automation
Thanks to AI and automation, quality control is more precise than ever. Smart manufacturing lines now use cameras, sensors, and data analytics to catch defects in real time.
This level of precision ensures that every radiator tank meets strict quality standards before it ever leaves the factory.
Conclusion: A New Era of Radiator Plastic Tanks
As you can see, the world of radiator plastic tank manufacturing isn’t stuck in the past. In fact, it’s one of the most innovative areas in automotive parts production today. From advanced materials and smart sensors to eco-friendly manufacturing and 3D prototyping, this humble component has undergone a serious transformation.
These innovations don’t just benefit automakers—they also mean better performance, fewer breakdowns, and more savings for everyday drivers like you.
So the next time you pop your car’s hood, take a second to appreciate that tough little tank. It's smarter, stronger, and more advanced than ever before.
Comments